Fasteners and Machining: Enhancing the Production Process
Fasteners and Machining: Enhancing the Production Process
Blog Article
Navigating the Globe of Fasteners and Machining: Approaches for Precision and Rate
In the complex realm of fasteners and machining, the mission for precision and speed is a continuous obstacle that demands precise interest to information and critical preparation. From recognizing the diverse array of fastener kinds to picking optimal materials that can endure extensive needs, each action in the procedure plays a pivotal role in accomplishing the preferred result.
Understanding Fastener Kind
When selecting fasteners for a project, understanding the various types offered is important for making certain ideal efficiency and integrity. Bolts are utilized with nuts to hold products together, while screws are flexible bolts that can be used with or without a nut, depending on the application. Washers are necessary for distributing the load of the bolt and protecting against damage to the material being secured.
Picking the Right Materials
Comprehending the value of selecting the best products is paramount in guaranteeing the optimum efficiency and reliability of the chosen bolt kinds discussed previously. When it comes to fasteners and machining applications, the product choice plays a vital duty in establishing the general toughness, longevity, rust resistance, and compatibility with the designated environment. Various materials supply varying buildings that can dramatically affect the performance of the fasteners.
Typical products utilized for bolts consist of steel, stainless-steel, titanium, brass, and aluminum, each having its distinct toughness and weak points. Steel is renowned for its high stamina and durability, making it ideal for a wide variety of applications. Stainless steel offers outstanding corrosion resistance, ideal for settings susceptible to moisture and chemicals. Light weight aluminum is corrosion-resistant and light-weight, making it ideal for applications where weight reduction is vital. Brass is commonly chosen for its aesthetic appeal and excellent conductivity. Titanium is recognized for its remarkable strength-to-weight proportion, making it suitable for high-performance applications. Choosing the best material entails thinking about elements such as toughness needs, ecological conditions, and spending plan restraints to make certain the preferred performance and longevity of the fasteners.
Precision Machining Techniques
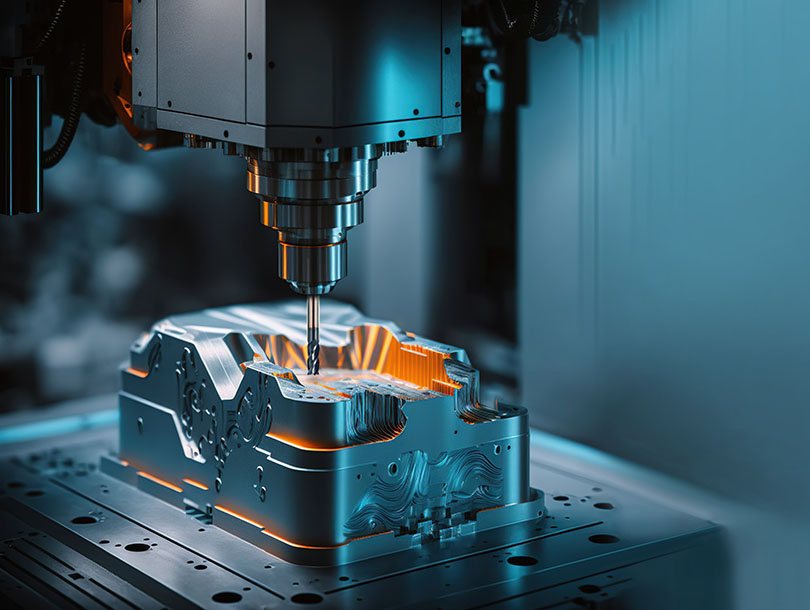
In enhancement to CNC machining, various other precision techniques like grinding, turning, milling, and boring play important roles in bolt manufacturing. Grinding aids attain great surface area i thought about this finishes and limited dimensional resistances, while turning is usually made use of to produce round parts with exact diameters. Milling and boring operations are necessary for forming and view developing openings in bolts, guaranteeing they meet precise specifications and feature correctly.
Enhancing Rate and Effectiveness
To enhance bolt production procedures, it is crucial to enhance procedures and carry out efficient methods that complement accuracy machining techniques. Automated systems can take care of repetitive jobs with accuracy and speed, permitting workers to focus on more complex and value-added activities. By incorporating these strategies, makers can achieve a balance in between rate and precision, eventually boosting their competitive side in the bolt industry.
High Quality Control Actions
Carrying out rigorous high quality control actions is vital in making sure the integrity and uniformity of fastener products in the production process. Quality control procedures incorporate numerous phases, beginning with the choice of basic materials to the last inspection of the completed bolts. One basic aspect of high quality control is performing comprehensive product examinations to verify compliance with specs. This entails assessing factors such as material strength, composition, and toughness to guarantee that the bolts fulfill industry standards. In addition, keeping an eye on the machining processes is crucial to promote dimensional precision and surface coating top quality. Utilizing innovative modern technology, such as automated assessment systems and accuracy measuring tools, can enhance the accuracy and effectiveness of quality assurance treatments.
Routine calibration of tools and machinery is imperative to preserve uniformity in manufacturing and guarantee that bolts meet the necessary resistances. Executing rigorous protocols for determining and resolving non-conformities or flaws is vital in avoiding substandard items from entering find out this here the market. By developing a thorough quality control structure, suppliers can support the track record of their brand name and supply bolts that meet the highest possible requirements of efficiency and sturdiness.
Conclusion
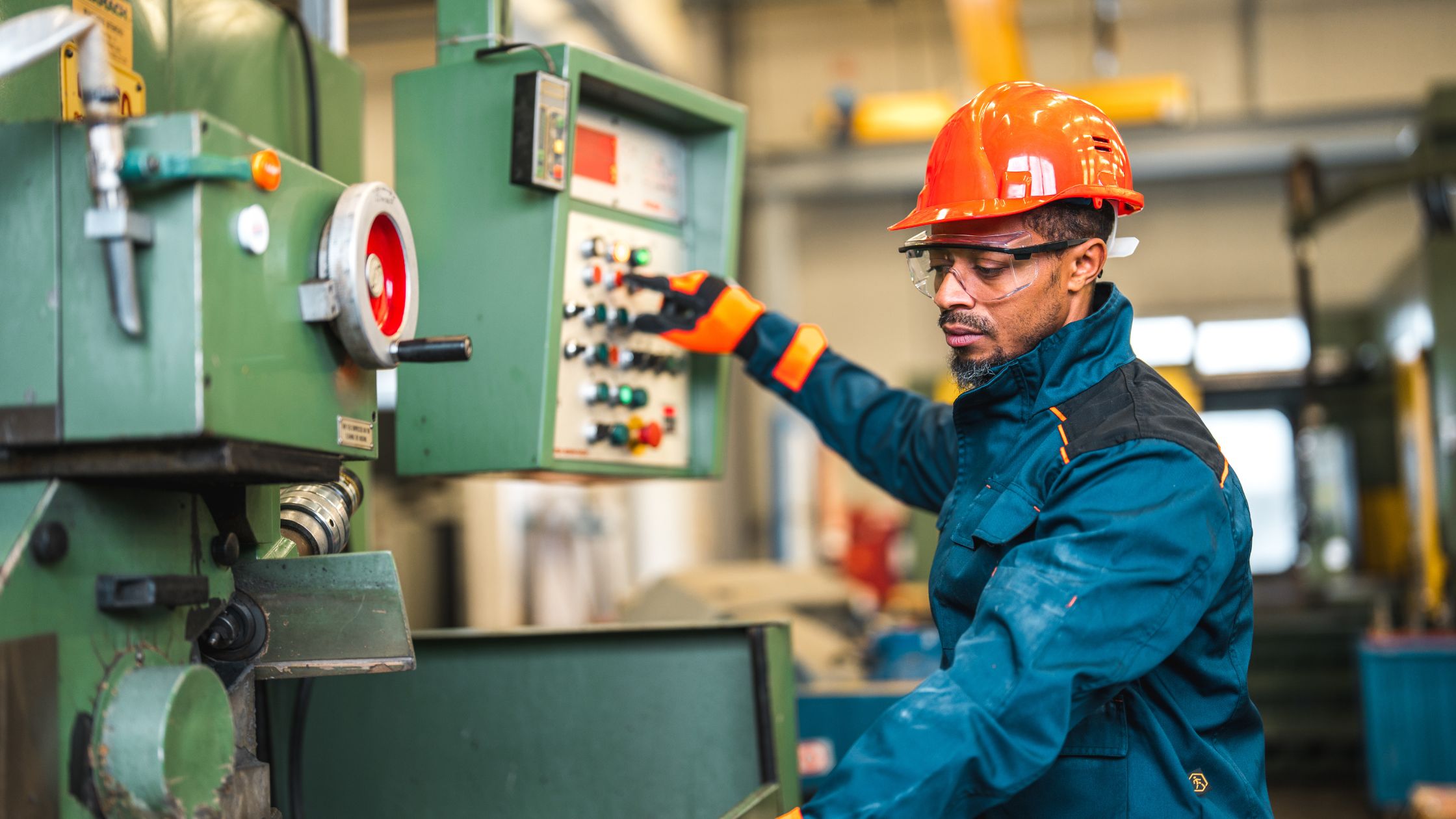
In the intricate realm of bolts and machining, the mission for accuracy and rate is a continuous difficulty that requires careful attention to detail and tactical planning. When it comes to fasteners and machining applications, the material choice plays a critical function in determining the overall stamina, durability, corrosion resistance, and compatibility with the intended environment. Accuracy machining involves numerous innovative techniques that ensure the limited resistances and requirements needed for bolts.In enhancement to CNC machining, other precision strategies like grinding, turning, milling, and drilling play important duties in fastener manufacturing.To enhance fastener production procedures, it is crucial to enhance operations and implement reliable methods that complement accuracy machining methods.
Report this page